Awareness of the environmental effects of industrial growth has intensified strive towards reduced carbon dioxide emissions. Indeed, modern society is increasingly concerned about energy efficiency because this aspect is linked to environmental degradation. Discussions about industrial energy often revolve around the gas turbine, a device that has been around ever since the era of water wheels and windmills. This highly reliable equipment converts heat into useful energy, but it is prone to degradation. Many users always wonder why the gas turbine performance degrades with time. This article covers this problem and gives approaches that can manage it. Gas Turbine Components and Degradation Potential The life of a gas turbine is hinged on various components of the equipment and the quality of maintenance that they receive. It is important to understand all these factors to be able to deal with gas turbine degradation appropriately. Gas turbine components can be categorized as:
- Turbine
- Inlet system
- Compressor
- Exhaust system
- Combustion area
- Base
- Support systems
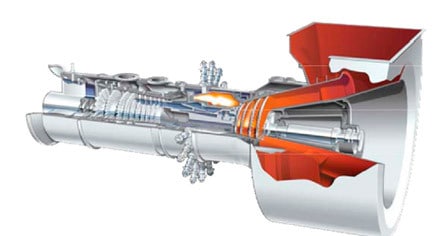
Fig 1. SGT-600 Gas Turbine, Araner
Over the lifetime of the equipment, any of these components can undergo tear and wear. Specially, the focus is on the aerodynamic parts that comprise of compressor, pump and turbine. The smooth cooperation of these components results in gas turbine function. Degradation on any of these areas can hamper performance significantly.
Contaminants
Airborne contaminants can find their way into the GT as either hard particles or soft particles. Hard particles that could cause erosion and fouling include carbon particles, ash, dust and sand. Soft particles are usually associated with fouling. They include industrial chemicals, air borne insects, unburnt hydrocarbons and soot. Most of these contaminants are less than 2μm in size. Note that selection of fuel is important -its constituents can affect performance and equipment life. Heavy hydrocarbon fuels have high level of radiant thermal energy, thus can degrade hardware significantly. Often, they contain corrosive elements such as lead, potassium and sodium. Slightly friendlier to the components are distillates, although they may still pose a challenge if contaminated during transport or on site.
Corrosion and Erosion
Flow path devices can lose their material due to chemical contaminants in the inlet air in a process called corrosion. Lead, vanadium, sodium are the leading elements in this regard. There is also the possibility of damage type of degradation, which involves larger foreign objects hitting components in the flow path of the gas turbine.
Fouling
We can define fouling as the adherence of particles on the annulus and airfoil surfaces that leads to degraded efficiency and flow capacity. Fouling in the gas turbine hampers performance through a number of alterations related to the inlet angle, surface roughness, throat opening and airfoil shape. Fouling is such a prominent issue for gas turbines that about 80% of performance issues that occur during operation are attributed to it.
Countering this Degradation Effectively
Engineers have developed various ways of mitigating the problems discussed above in pursuit of gas turbine optimization. Chief among them are proper maintenance practices. Keeping the control system in good shape is one of the best remedies. With a reliable control system, engineers are able to keep fuel scheduling in check to avoid unnecessary temperature gradients. Compressor cleaning and Inlet Filter System inspection are other essential maintenance steps. Alongside these basic interventions, the following approaches are recommendable to take control of the gas turbine degradation curve:
- Application of clean steam/water and fuels
- Close monitoring of gas turbine degradation
- Inlet filtration system should match the site conditions
- Employment of reliable maintenance/operating procedures
- Prompt execution of necessary remedial actions
- Use the best coated surfaces for compressor
Turbine Inlet Air Cooling
Similar to the factors identified above, high ambient temperatures can degrade turbine performance significantly. Yes, one can address higher demand for power with additional generators, but this is an expensive remedy as compared to turbine inlet air cooling (TIAC). TIAC improves the performance of existing gas turbines by up to 30%. Delivery of consistent cooling capacity not only promotes optimal power output, but also enhances gas turbine life. The beauty of TIAC technology from ARANER is that it is applicable for both existing and new gas turbine power plants. The secret to get desirable results is to adhere to natural steps of TIAC design as can be derived from this eBook. Some of the suggested parameters for optimum plant performance are ambient conditions, desired air cooling, thermal energy storage, heat rejection type and centralized/individual plant. Drawing from our experience in the Middle East, ambient air conditions are significant factors for gas turbine degradation (whether the unit is single or combined cycle). We have derived several realities, starting with the fact that tailor made turbine cooling systems are the best for clients in the Middle East and other comparable regions. For instance, the high temperature and humidity is corrosive for some materials that would otherwise work perfectly in the West.
Fig 2. Interior of a TIAC cooling system, Araner
Conclusion
For equipment as critical as the gas turbine, any form of degradation is serious. While the turbine is prone to deterioration as is the case for any other engineering device, steps to minimize or even stall the process, exist. Any owner interested in high availability of his machine must understand the factors that affect its performance. The manufacturer may provide the necessary maintenance recommendations, but only proper operator training, regular inspection, and rigorous analysis of systems will guarantee peak performance. For further details on how to solve problems with gas turbine degradation in a turbine cooling system and related aspects, call us today.