You recognize that all types of power plants (gas based, coal-fired or oil) prioritize temperature control for operational reliability. It is also true that industries have different requirements and specifications regarding temperature control for their environments or products. ARANER deals with a wide range of industries, most of which need constant regulation of temperature conditions. For example, the operations within the food & beverage industry fall under the regulation of the FDA (Food and Drug Administration) and similar bodies. Healthcare, retail industry and power generation are also closely monitored. As expected, years and years of control in our area of interest-, power generation- has led to the development of best practices. Adhering to the best practices is good for not only reducing costs, but also minimizing risks in the plants among other benefits. These will come out clearer in a while as we discuss a few best practices of temperature control technology in power plants.
Power Plants – Need for Temperature Control
The main operating parameters in a thermal power plant are:
- Generation efficiency
- Plant load factor (PLF)
- Heat rate
- Auxiliary power consumption
- GHG emissions
Temperature touches on virtually all of these elements; hence, it is understandably a widely measured component in the power plant. Unfortunately, poor measurement may occur because of nonlinearity or electrical effects and cause massive damage to equipment. Modern instrumentation for temperature control comes in handy in pointing out an existing problem, its location and the possible remedies in good time. Despite the wide adoption of power generation, many would-be power generation investors/ managers are faced with numerous challenges. More often than not, they are ill prepared to handle the problems even when power generation is their primary business. We believe that this review of some best practices of temperature control technology in the industry will be of great help.
Three Best Practices of Temperature Control
-
Transmitters in Place of Direct Wiring
Often, engineers will wire temperature sensors to the control system using direct wiring. They do this because they hold the wrong view that this option is easier and cheaper. Although most facilities have direct wiring installed, the best practice today is leaning towards installing transmitters instead. Benefits of transmitters are less money and time for installation, higher uptime, increased measurement reliability and less maintenance. You will be pleased to note that transmitters provide the choice for Foundation Fieldbus, Profibus, HART and similar digital communication protocols. Using a twisted pair wire to transmit these outputs for longer distances is an irresistible feature. Direct wiring can be extremely expensive because it uses the expensive and fragile sensor extension wires. Considering that temperature sensors and automation system in a power plant can be several hundred feet apart, you realize the kind of savings transmitters have introduced ever since their introduction.
Fig 1: Temperature Transmitter and Sensor in a Power Plant
Transmitter technology advancement compared to a few years ago is also something worth noting. Smart transmitters come with a backup function that reduces down time considerably. It is safe to say that transmitters are the best bet for accommodating future advances in technology advances.
-
Thermocouples and Resistance Temperature Detectors (RTDs)
Infrared sensors may be applied in specialty measurements, but the vast majority of temperature control in power plants is based on either thermocouples (T/Cs) or resistance temperature detectors (RTDs). Each of these components presents unique advantages and disadvantages, so they are applicable in power plants. Where repeatability and accuracy is of chief concern, RTDs are more suitable. A stable output and an accuracy of 0.1ºC make up for the limited range of this technology. The main drawback of this technology is costliness compared to thermocouple technology. An equally physically configured thermocouple will cost about five times less. If you are looking for a device suited for specific conditions and temperatures, then you may want to choose a thermocouple. Some are even designed for temperatures up to 3100°F. Their instability, especially at elevated temperatures, is their main undoing.
-
Temperature Control Around Steam Loop
Safety concerns have hampered efforts to maximize boiler operation for a long time. A temperature increase of 50°F within the boiler may duplicate the chemical process. Uncontrolled chemical processes such as this one affect the operational life and efficiency of the plant. Remember that boiler plant can operate at as high as 600-bar pressure, which presents safety challenges. The best practice to take care of these concerns is to measure pressure and temperature around the steam loop. Ask ARANER specialists in temperature control technology to help you deploy measuring devices around critical areas for example:
- Boiler
- Steam Line
- Cooling Water System
- Stack
- De-aerator Plant
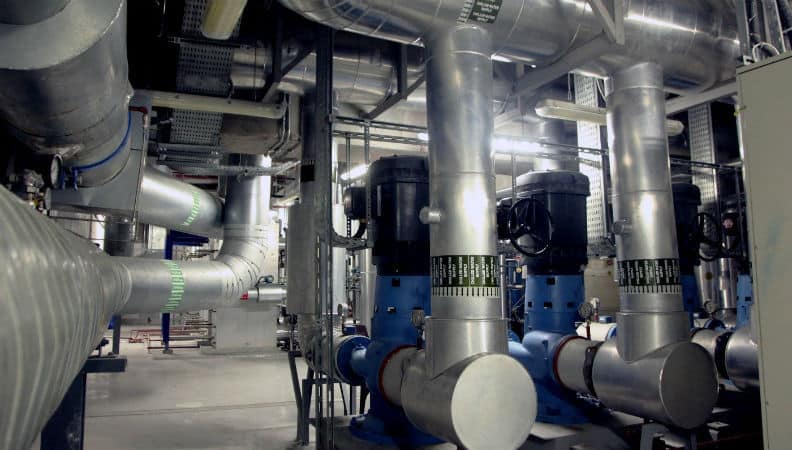
To Wrap Up
A host of best practices, whose idea is to reduce system costs, eliminate noise and increase accuracy, defines power plant temperature control. Following the provided guidelines allows enables the plant to have some level of flexibility. Modern temperature control technology is designed for timely diagnosis of common problems. For these reasons, modern instrumentation has greatly enhanced temperature measurement and control in power plants across the globe. You do not want your power plant to shut down and incur costs running into millions simply because a temperature sensor failed. Best practices help you anticipate failure and deal with it before it occurs. Talk to us for more about the kind of technology available.