Why Footprint Optimization?
One of the most critical points faced by engineers when developing the basis of a District Cooling and Heating plant (DCHP) is the footprint optimization.
Footprint optimization, as its name indicates, consists in the best use of available space by reducing the constructed area, the exploitation of free spaces together with a logical distribution of the different rooms and compartments required. Optimizing the plant footprint is a necessary but challenging pursuit for any contractor. It's necessary to ensure that the contractor is making the best use of its assets to meet demand and enhance profitability.
Many are the reasons to focus all the efforts in the 1st design stage of a District Cooling and Heating plants (DCHP) resulting in optimized design:
- Economically: It is easily understood that the less m2 of area required, the more savings of construction; less concrete, less manpower, shorter construction time and so on. Indirectly it will also affect some other works such as electrical, HVAC, maintenance, housekeeping, etc.
- Municipality normative: DCHP normally are located in urban areas. Sometimes in these areas there are restrictions in terms of design; limited area for installing the DCHP, limited height by the surrounding buildings or architectural restrictions to not break with the neighbourhood design with an industrial plant (DCHP).
- Contract terms: It’s also very common to have “limited space” defined in the contract since the bidding stage. If so, the best engineering practice are required to comply with the contract with no deviation.
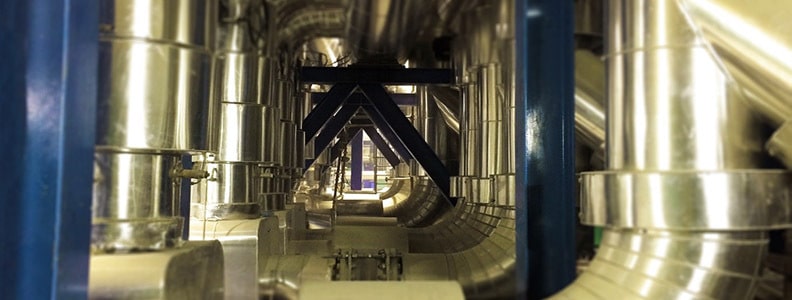
Main Guidelines for Footprint Optimization
Whatever the reason to seek for footprint optimization, the following steps or principles may help if they are taken into consideration by any contractor or project consultant:
- Calculate the dimension of main equipment: Mechanical, electrical, I&C, etc.
- Civil calculations for structural and foundation design, beams configuration and its location
- Calculate and establish the area required for the normal operation of the main equipment: Mechanical, electrical and control rooms, offices, workshops, storages, etc.
Based on best engineering practices, these areas shall be enough to operate the plant without interferences within the different equipment.
- Design the DCHP in such a way the distance for interconnections within equipment and dedicated rooms are minimal.
- Calculation and designing of DCHP maintenance areas.
- Calculate and design emergency exits and escape routes without obstacles in between.
- Design of mezzanines for cable pulling, pipe routing and HVAC ducts.
- Study the groundwater table to consider basements or floors above ground in the design.
- Define the services and facilities to be included in the DCHP: Offices, meeting rooms, lobbies, bathrooms and others.
- Well designed and located stairwells taking advantage of dead spaces.
- Correct technology selection
Technology Selection
Let's stop at this point that may be the key to awarding the project and one of the challenges to overcome. Araner as DCHP specialist uses at this stage much of his resources from the R&D department.
The correct selection of the technology besides being an important point to achieve the highest overall plant efficiency, it is important at the time of footprint optimization. Depending on the technology selected, the number of boilers, pumps, compressors, motors, cooling towers, air condensers and secondary equipment may be affected and therefore the area used to locate, feed, control and operate these may be increased or reduced directly affecting the DCHP design and its footprint. For that, Araner is always collaborating with contractors, consultants or final clients to study, design and develop their DCHP under any specifications and contract terms.
The most important point is to design the system to reuse the maximum heat dissipation to the district heating network having a heat pump working for cooling load and heating load simultaneously.
In the following animation you will easily identify how a good selection in the technology, like the direct condensation, may reduce the required space for the mechanical equipment.
Figure 1: Traditional water cool condensation Vs Araner Direct Condensation
When both loads are managed by the same refrigeration equipment the boilers and the heat dissipation systems (cooling towers or air cooled condenser) will be reduced only for back-up in case of the heating peak mode or for the summer time in cooling peak mode.
The best footprint reduction appears when no equipment is needed nor installed.
When selecting direct condensation technology the refrigerant circuit is reduced considerably. Inside the area typically designed for a traditional chiller, two direct condensation chillers can be installed.
Besides, you will save the condenser pumps for pumping the water to the traditional cooling towers. These condenser pumps in addition to occupying much area in your DCHP also affect in a negative way to the total plant efficiency because of their normal high consumption.
And finally, more savings are coming from reducing the pipe sizes. The water pipes are wider than those carrying refrigerant to the evaporative condenser.
For all that reasons, plus saving electrical jobs and others, the selection of technology is a very important aspect to consider.
Benefits and Success of a Proper Footprint Optimization
With all above variables evaluated the benefits and success of a proper optimization are very easy to identify:
- Project profitability:
- Up to 40% of savings in construction / installation.
- 30 % in footprint reduction.
- 35% reduction in required site manpower.
- The machinery cooling and heating may be reduced.
- A logic interconnection within items may result in reduced costs.
- Improvement in the use of the building: Studying the DCHP from all departments (Civil, Mechanical, Electrical, O&M operators and Management) could end in an optimized design and reduced footprint when actually the different working areas are or seems bigger; eliminating: Unnecessary spaces, complicated designs, large corridors, dead spaces, etc…
- Project deadline: It may be improved in same proportion as civil works are reduced
The points above in combination can lead to the award of the project and the success of all engineering team efforts!
ARANER Footprint Optimization Real Example:
DCHP height optimization and improved use of the building
The following case was a real Project where Araner was requested to prepare their alternative for a DCHP with 90,000 TR of Cooling Capacity.
Araner with its experience was able to design the DCHP reducing in two floors the whole plant. It was achieved due to the correct equipment selection and technology to be used.
ARANER design
Other Design
It supposed of course a benefit in terms of construction, the project became more profitable, minor civil works, minor risks… and an improvement in the plant efficiency going from 0.78 kW/TR to 0.72 kW/TR.
Do you want to learn more about our Footprint optimization solutions? Do you need improvements in a power plant? Visit our website or contact us. Our experts will be available to assist you!!